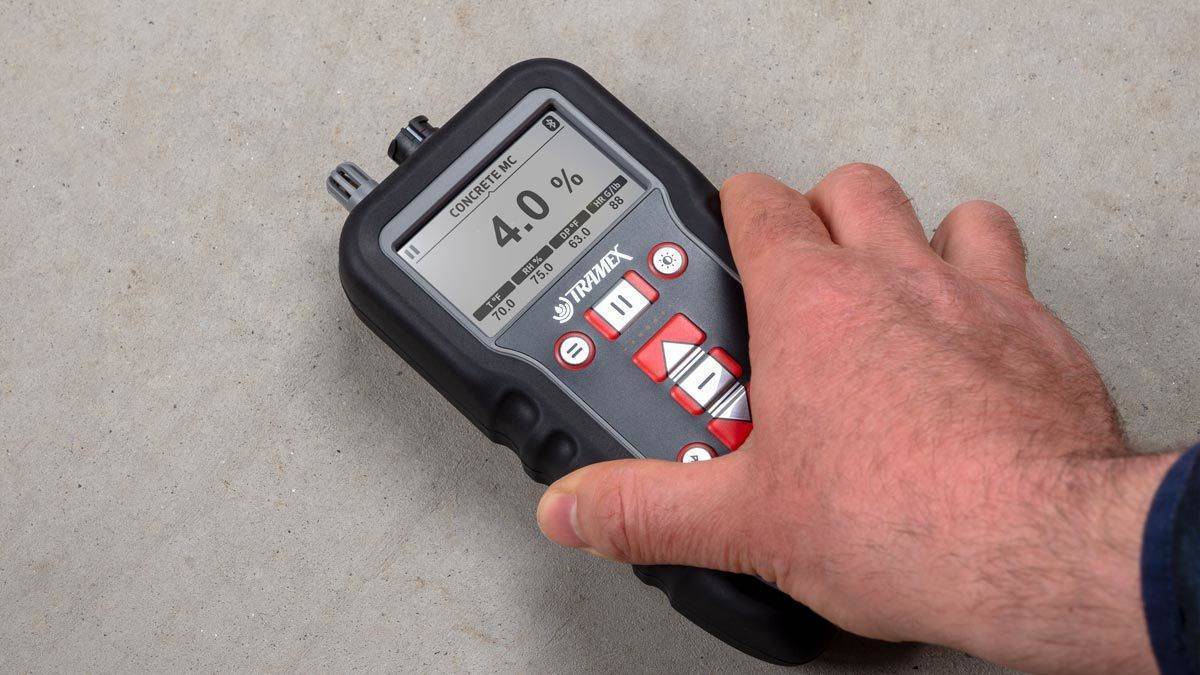
When drying concrete after water intrusions it is important to monitor and measure the moisture content of the concrete in two phases:
- during the drying phase
- after the drying is complete
This allows the restorer to establish valuable knowledge of how the drying process is progressing and, once the drying process is complete and the concrete has been brought back to pre-loss conditions, decide what mitigation, if any, will be required before reinstalling a floor covering.
Understanding testing methods
In order to monitor and measure the moisture content of the concrete in a meaningful way the restorer needs to understand the different test methods, the meaning of their results and how they relate to the restoration industry compared to the flooring industry for which these test methods have been developed.
This is an important point to keep in mind because the testing methods prescribed were designed for the flooring industry to test the drying process of newly poured concrete and establish when it is dry enough to receive a floor coating or covering.
This is different to the restoration industry as the goal here is to dry the concrete back to pre loss conditions. Equilibrium Relative Humidity as per ASTM F2170, Calcium Chloride vapor emission testing as per ASTM F1869 and non-destructive Electrical Impedance measurement as per ASTM F2659 are the most commonly specified tests for measuring the moisture in concrete in the United States.
F2170 and F1869 are both considered quantitative tests whereas F2659 is considered qualitative and while the differences are about how the tests are perceived rather than what they are actually measuring, this will mean that most flooring manufacturers will require that either F2170 or F1869 are carried out before a floor can be installed.
Both F2170 and F1869 both measure the water vapor, not the moisture content, in concrete and as such they are very impractical tests to carry out during the drying phase as they require the building to be in service condition for at least 48 hours before the testing can begin. This is due to the fact that changing environmental conditions will affect the relationship between the water vapor and the water.
Most tests which have been developed for the flooring industry are designed to measure the construction moisture within the concrete and not the moisture from intrusion or other external sources.
As such it is important to be able to distinguish between the different sources when inspecting concrete after water damage, and the best way to do this is to look at the results from a variety of test methods. The restorer needs to be able to identify:
- background moisture which could either be from construction moisture still in the slab,
- moisture which is still entering a slab from beneath if there is an insufficient sub floor sealer,
- moisture from above if there are dew point issues or leaks in the building.
Without this understanding it is common for restorers to attempt to dry against nature and waste a lot of energy drying moisture which will possibly return after the drying has been completed. This is especially important if the moisture is coming from beneath the concrete due to the absence of a sealer.
Monitoring the drying process
By using an electrical impedance device, which gives instant and repeatable results, to map and monitor the moisture during the drying phase, a restorer is able to focus on the changes in readings rather than the readings themselves.
At the beginning of the drying process the moisture content readings will be high and should rapidly reduce as the drying progresses. As the drying progresses the difference between readings over time will decrease and this will help determine when the drying is complete.
The mapping of these readings will also indicate where to test further once the building is back in an in-service condition, using either Relative Humidity testing as per ASTM F2170 or Vapor Emission testing as per ASTM F1869. If the impedance device used indicates a percentage moisture content value (MC%) of the slab then this information can be very useful when further testing with Equilibrium Relative Humidity testing.
For example: Relative Humidity testing per F2170, when used as a stand-alone test, is prone to giving false positive or negative readings such as:
-
possibly false negative readings due to the quality of the concrete
-
false positive readings due to the concrete having less air movement when it is of a high quality
-
false negative readings due to uncured materials such as salts lowering the equilibrium relative humidity.
If the results of the non-destructive impedance test and the Relative Humidity test do not concur then it is possible to do further simple testing which can complete the information needed.
The essential testing methods
The combination of ambient testing, surface concrete temperature testing, in-situ RH testing and non-destructive impedance testing will cover the majority of the testing needs, with calcium chloride testing only used when the results of the others do not concur.
The use of multiple, yet simple testing methods allows for a complete picture of the moisture condition of the slab. The approach of marketing one test method over another has, in my view, done a disservice to the industry. The combination of tests helps draw a much better and more complete picture, as long as it is clearly understood what exactly is being measured with each test method and how they can be affected by the different ambient conditions that arise during the entire restoration process.
By Andrew Rynhart, CEO, Tramex Ltd. This article was first published in "Restoration & Remediation Magazine, August 2016 Issue.